A hazardous risk and safety assessment is vital for identifying potential dangers in the workplace and implementing appropriate measures to mitigate them. By having hazardous materials consultants conduct a comprehensive review, employers can safeguard the health and well-being of their employees, comply with Occupational Health & Safety (OHS) regulations, and create a safer work environment. This blog post will outline the steps in conducting a hazardous risk and safety assessment, providing valuable insights for employers and safety professionals.
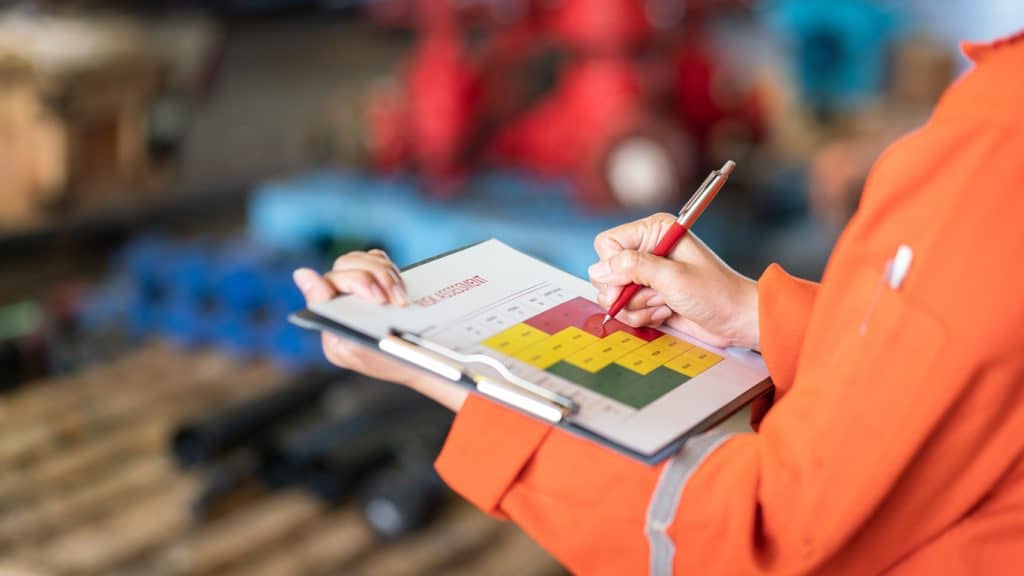
Step #1 – Identify Hazards
The first step in conducting a hazardous risk and safety assessment is identifying potential workplace hazards. It thoroughly examines the physical environment, equipment, materials, processes, and work practices. Consider factors such as chemical substances, machinery, electrical systems, ergonomic conditions, and potential sources of fire or explosions. Engage with employees, supervisors, and safety representatives to gather their input and observations on potential hazards. Additionally, consult relevant regulations, industry standards, and best practices to ensure comprehensive hazard identification.
Step #2 – Assess Risks
Once hazards are identified, the next step is to assess the associated risks. Evaluate the likelihood and severity of each hazard, considering factors such as frequency of exposure, potential harm to individuals, and possible consequences. This assessment helps prioritize risks and allocate resources effectively. Risk assessment tools, such as risk matrices or qualitative/quantitative analysis methods, are used to quantify and rank risks. Assign numerical values or categories to likelihood and severity to determine the overall risk level. This step enables the identification of high-risk areas that require immediate attention and the implementation of appropriate control measures.
Step #3 – Implement Control Measures
After identifying and assessing risks, it is crucial to implement control measures to minimize or eliminate hazards. Start with the hierarchy of controls, which includes elimination, substitution, engineering controls, administrative controls, and personal protective equipment (PPE). Depending on the nature of the hazards, control measures can involve modifying work processes, implementing safety protocols, providing training, installing safety equipment, or improving ventilation systems. Engage employees and safety representatives to ensure their involvement in the implementation process and foster a safety culture within the organization.
Step #4 – Regular Monitoring & Review
A hazardous risk and safety assessment is an ongoing process. Regular monitoring and review are essential to ensure the effectiveness of control measures and identify any new hazards or changing circumstances. Conduct inspections, audits, and observations to assess compliance with safety protocols and identify areas for improvement. Encourage employees to report near-misses, incidents, or concerns regarding safety. Review incident reports, analyze trends, and take corrective actions promptly. Stay updated with regulatory requirements and industry advancements to enhance safety practices continuously. Incorporate feedback from employees and safety professionals to refine control measures and maintain a proactive approach to workplace safety.
Step #5 – Engage Hazardous Materials Consultants
Engaging qualified hazardous materials consultants can significantly enhance the effectiveness of your hazardous risk and safety assessment. These professionals possess in-depth knowledge of chemical hazards, regulatory compliance, and industry best practices. They can conduct specialized assessments, such as air quality monitoring, exposure or hazardous materials assessments. For example, after hazardous materials assessments, they can provide guidance on implementing appropriate control measures, assist with employee training programs, and help develop emergency response plans. Their expertise ensures a comprehensive evaluation of risks and the implementation of tailored solutions, ultimately enhancing the safety culture and minimizing the potential for accidents or occupational illnesses.
Final Thoughts
Conducting a hazardous risk and safety assessment is essential for maintaining a safe work environment. Employers can protect their employees and meet regulatory requirements by identifying hazards, assessing risks, implementing control measures, and regularly monitoring and reviewing safety practices. Engaging hazardous materials consultants adds valuable expertise to the assessment process, ensuring comprehensive evaluations and tailored solutions.
Alberta Safety & Environmental Services (ASE Services) is one of the most reputable providers of Hazardous materials assessment and hygiene inspection services—including asbestos, lead, mould, mercury, and silica detection, as well as industrial hygiene testing for grow ops and other facilities. With a background in Alberta’s Occupational Health & Safety Commission and professional project management skills, our qualified staff can provide reliable handling of air quality and industrial hygiene from initial industrial inspection all the way to remediation programs. Whether just for a permit, or in-depth air quality control, we can help. Feel free to reach out and secure air quality and hygiene requirements for your building.