A safe and healthy work environment is crucial for employees’ well-being and any organization’s overall success. However, all hazardous materials consultants can tell you that workplaces are not devoid of risks and hazards. Understanding these risks and hazards is the first step toward effectively addressing and mitigating them. This blog post will explore common workplace risks and hazards and their characteristics and provide insights into creating a safer work environment.
Types of Hazards Checked By Hazardous Materials Consultants
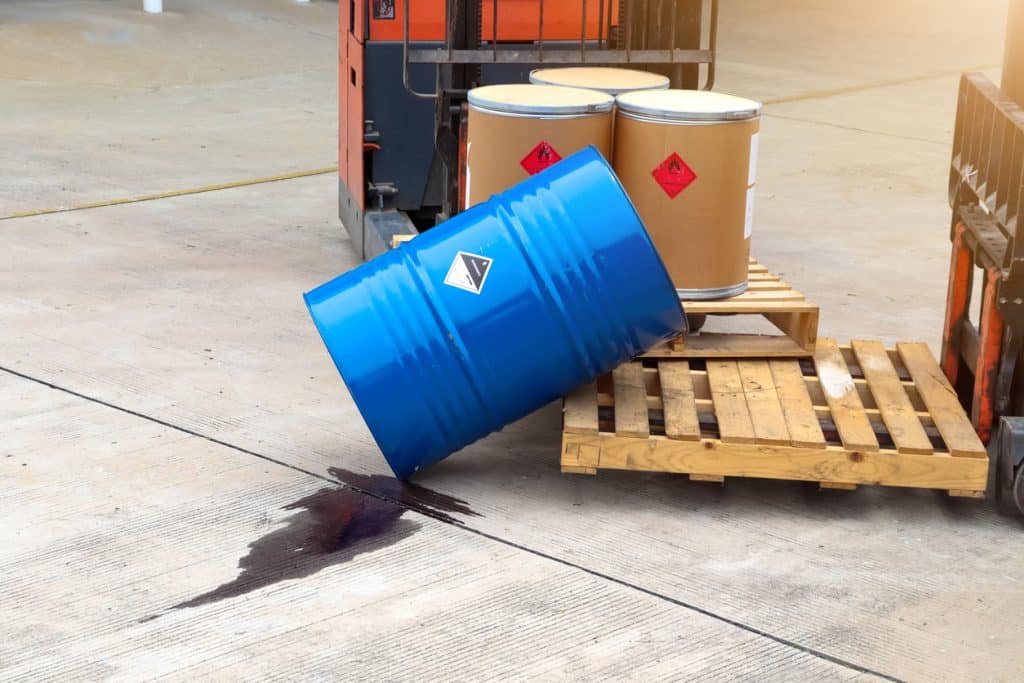
Physical Hazards
Physical hazards are among the most visible and easily recognizable risks in the workplace. They include slips, trips, and falls resulting from wet or cluttered floors, uneven surfaces, or inadequate lighting. Improperly maintained equipment, machinery, or tools can also threaten employee safety. Employers should regularly inspect their premises to identify and address physical hazards promptly. Implementing proper signage, providing personal protective equipment (PPE), getting noise assessments done, and establishing clear equipment maintenance and storage protocols can significantly reduce the likelihood of accidents.
Chemical Hazards
Chemical hazards are prevalent in various industries, including manufacturing, healthcare, and laboratories. These hazards involve exposure to harmful substances such as toxic gases, corrosive liquids, or hazardous materials. Workers who handle or come into contact with chemicals without appropriate protection are at risk of adverse health effects. For instance, if materials such as lead, mercury, or PCB exist in your workplace, they can be a hazard if not identified and controlled early on.
Employers need to provide comprehensive training on handling and storing chemicals safely. The first step to tackling chemical hazards is via hazardous materials assessments. Occupational Health & Safety (OHS) states that hazardous materials within a workspace be identified and properly controlled. Hazardous materials assessments ensure you address them by implementing proper ventilation systems, utilizing personal protective equipment, or establishing protocols for safe chemical handling, storage, and disposal, which are critical steps in mitigating chemical hazards.
Biological Hazards
Biological hazards are present in workplaces where employees are exposed to bacteria, viruses, mould, or other microorganisms. Industries such as healthcare, laboratories, and agriculture often face these risks. Biological hazards include exposure to bloodborne pathogens, airborne diseases, or hazardous animal waste. Implementing infection control measures, providing appropriate vaccines and protective clothing, and educating employees about proper hygiene practices can help minimize the risk of biological hazards. Regular cleaning and disinfection of work areas and proper waste management are also vital in preventing the spread of infectious diseases.
Ergonomic Hazards
Ergonomic hazards arise from improper workstation design, repetitive tasks, or poor posture. These hazards can result in musculoskeletal disorders, including back pain, carpal tunnel syndrome, or strains. Employers should assess workstations and make adjustments to ensure ergonomic comfort and promote good posture. Providing ergonomic furniture and adjustable equipment and encouraging regular breaks and stretching exercises can help mitigate ergonomic hazards. Training employees on proper lifting techniques and promoting awareness of ergonomic principles are crucial to creating a safer work environment.
Psychological Hazards
Psychological or psychosocial hazards impact employees’ mental health and well-being. These hazards include excessive work demands, workplace violence, bullying, or inadequate support systems. Such hazards can result from high-stress levels, burnout, and decreased productivity. Employers should prioritize employee mental health by fostering a supportive work culture, providing resources for stress management, and promoting work-life balance. Open communication channels, conflict resolution mechanisms, and employee assistance programs can help address and mitigate psychological hazards.
Final Thoughts
Recognizing workplace risks and hazards is essential for creating a safe and healthy work environment. By understanding the characteristics of physical, chemical, biological, ergonomic, and psychological hazards, employers can implement appropriate measures to mitigate risks, like conducting hazardous materials assessments, which can protect employee well-being. Regular risk assessments from hazardous materials consultants, comprehensive training, proper maintenance protocols, and the provision of necessary protective equipment are crucial elements in minimizing workplace hazards. Prioritizing employee safety ensures a healthier workforce and increases productivity and organizational success.
Alberta Safety & Environmental Services (ASE Services) is one of the most reputable providers of Hazardous materials assessment and hygiene inspection services—including asbestos, lead, mould, mercury, and silica detection, as well as industrial hygiene testing for grow ops and other facilities. With a background in Alberta’s Occupational Health & Safety Commission and professional project management skills, our qualified staff can provide reliable handling of air quality and industrial hygiene from initial industrial inspection all the way to remediation programs. Whether just for a permit, or in-depth air quality control, we can help. Feel free to reach out and secure air quality and hygiene requirements for your building.